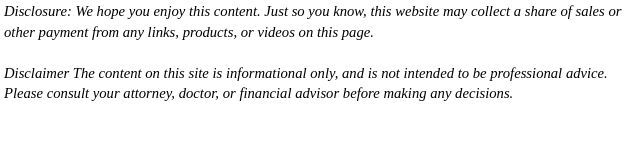
Welding is difficult and requires specialized tools. Electric welding equipment actually changes frequently. Professional welders will have to learn how to operate new tools relatively consistently. They’ll already need to use brazing torches and robotic types of welding equipment now.
Cutting and welding equipment is becoming more efficient, but it can still be unsafe to use without the right safety procedures and items. Welders also have to be careful about the heavy metals contained in the fumes that are produced as part of the welding process.
The best type of welder will be familiar with multiple modern tech pieces. They’ll have more options as professional fabricators that way.
The process of fabrication in welding can be performed very successfully. Welders can work with many materials and input voltages. They can also use different welding procedures to accomplish slightly different forms of product fabrication.
Welders frequently work in the construction industry. The people entering this field will find lots of jobs there. Similarly, the automotive industry needs many professional welders. Other welding professionals work in the aerospace world, although people will compete for those assignments. The energy industry, including emerging parts of that field, also employs plenty of experienced welding workers.
Are you more interested in a trade school education rather than traditional college choices? Are you consider attending welding school to quickly learn a trade and enter the workforce? Do you have questions about the usual welding career path tree and what opportunities can lie ahead of you after graduation? If so, then finding a local welding program at a community college or technical college may be the best option for you at this time.
In these kinds of programs, you will learn all the basics and get the foundation you need to expand your welding career path. You will start with small welding tool setups and applications and move on to larger and more complicated procedures and processes as you progress through the training. The school will provide the basics and help you get the tools and stick welding supplies you need to learn the craft and perfect your skills.
When looking for a welding school to attend or a program to enroll in, be sure you find one that is accredited by and connected to a local or national welding association, so you can be sure you are getting a quality education right from the start!
The earliest evidence of welding was traced back to 3,500 B.C. Thousands of years later, a large percentage of manufactured products continue to require welding. In the United States alone, over 50% of the products made within this country are welded together. Due to this requirement, it’s not surprising that the manufacturing industry is expected to experience growth.
Projected Growth Within the Manufacturing Field
Currently, two out of every three welding jobs are in the manufacturing industry. Recent data shows that this amounts to over 500,000 employed welders, according to the American Welding Society. The U.S. Bureau of Labor Statistics reported that the demand for welders and workers with related skill sets is expected to increase. By 2024, projections indicate that 412,300 jobs will be available for these types of jobs:
-
- Welders
- Cutters
<Solderers
Brazers
The Importance of Updating Manufacturing Methods
Many companies continue to use outdated methods to manufacture products. As a result, thousands of dollars in labor are lost every year. Using outdated methods to align pipes and fittings are just one example of this. Alignment clamps, in particular, have undergone improvement. Currently, there are five different types available that can address every aspect of aligning pipes and fittings.
The Importance of Maintaining a Safe Work Environment
Since the manufacturing industry can be a dangerous work environment, it’s important to follow regulations to the letter. In order to increase safety, for example, workers can use non sparking tools for welding. There are other types of non sparking hand tools, such as non sparking wrenches. When considering the importance of using non sparking tools for welding, it makes sense for workers to have entire non sparking tool kits available.
Learn More About Non-Sparking Tools and Other Advancements
When your company contacts suppliers for non sparking tools, they can learn more about non sparking hand tools and other supplies that they may need. Since using non-sparking tools can assist with reducing workplace injuries, it can also cut down on employee absenteeism and the costs associated with this. Furthermore, since successful businesses tend to be those that remain informed on updated manufacturing methods and tools, this can potentially make an impact on your overall business growth.